Every company’s number one concern should be the safety of employees in the workplace, and they should follow standards devised by OSHA (Occupational Safety and Health Administration). Addressing potential hazards and knowing how to properly store hazardous elements is one of the main things every company should do. Creating a safe facility for employees is common sense, but remember that OSHA regulations are much more than that.
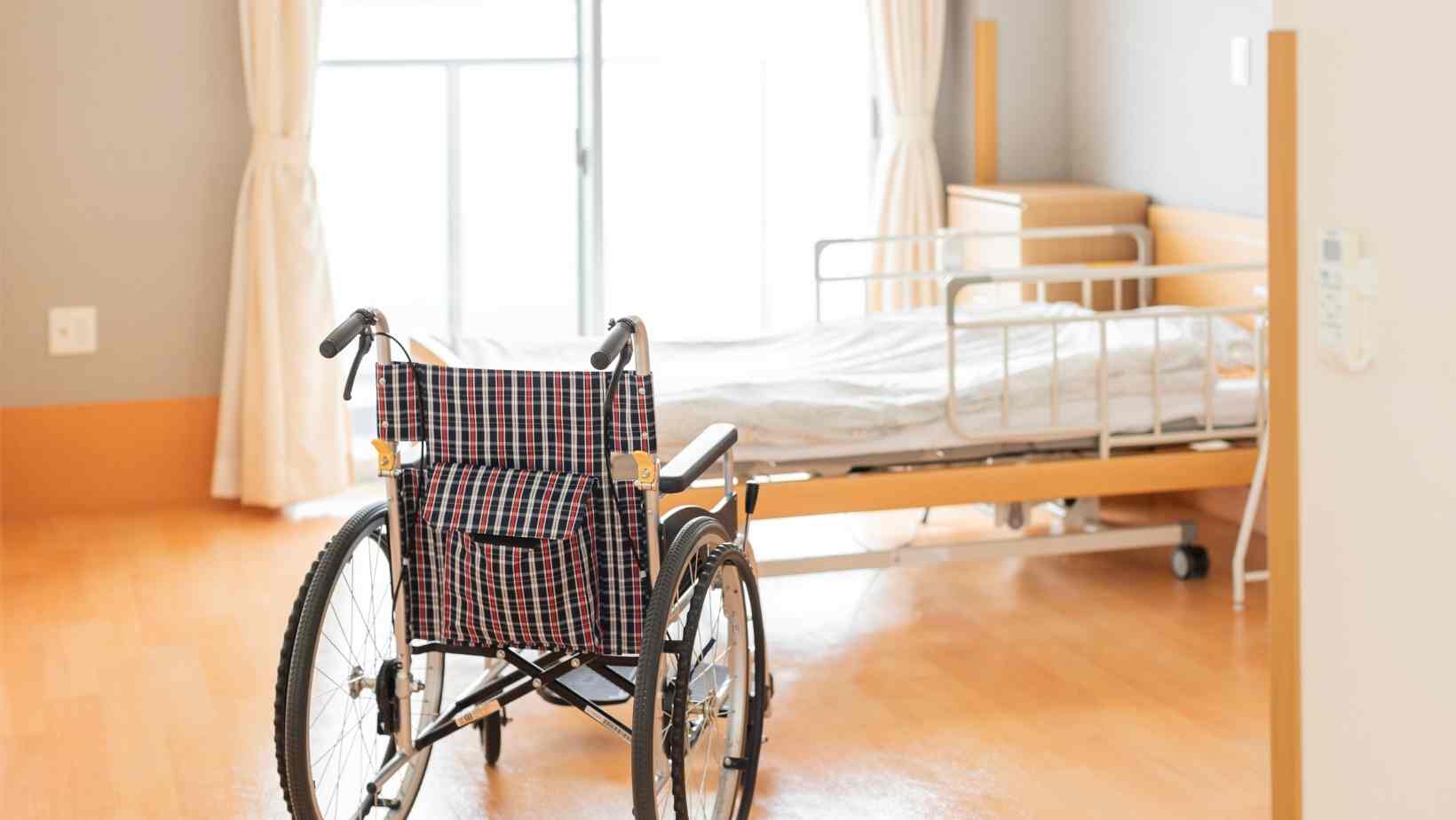
Below we will break down some of the most important things every company should provide.
Jump to:
Mark potential hazards
Some industries require using hazardous materials necessary for regular operation. Seeing dangerous equipment and harmful chemicals in some industries is not unusual. To keep the facility safe, it’s crucial to mark those potential hazards so employees know how to protect themselves from injury. Also, you must use color, labels, and posters, and store flammable liquids in appropriate containers.
If you don’t intend on spending too much on storage cans, you might find metal gas cans for sale, and also flammable liquids containers, and other biohazard containers that will help you keep your personnel and facilities protected. Follow OSHA instructions to use proper containers, and see whether you’ll need type I safety cans, type II safety cans, DOT-approved cans, oily waste cans, disposable cans, or others.
Emergency procedures
You must have emergency procedures in place, meaning you need to comply with every OSHA standard to ensure the safety of your employees. Emergency procedures mean having a set of actions required by employees in case of emergencies. For example, fire is a common hazard in every type of facility, so you must provide fire safety. Make sure you have plans and procedures in place to prevent such hazardous situations.
You must have marked exits, and a fully stocked first aid kit, and depending on the workplace, some facilities even require medical personnel on-site. Note that the OSHA requires workplaces with 10 or more employees to have a written emergency action plan, so it would be best to schedule a facility-wide emergency meeting to explain the action plan and if needed provide training for the employees.
Protective equipment and maintenance
Every employer should provide their employees with the necessary PPE including masks, proper clothing, protective eyewear, noise protection, and respirators. Employees who work at great heights should have fall protection. However, OSHA prefers employees to keep out of any situation that requires PPE.
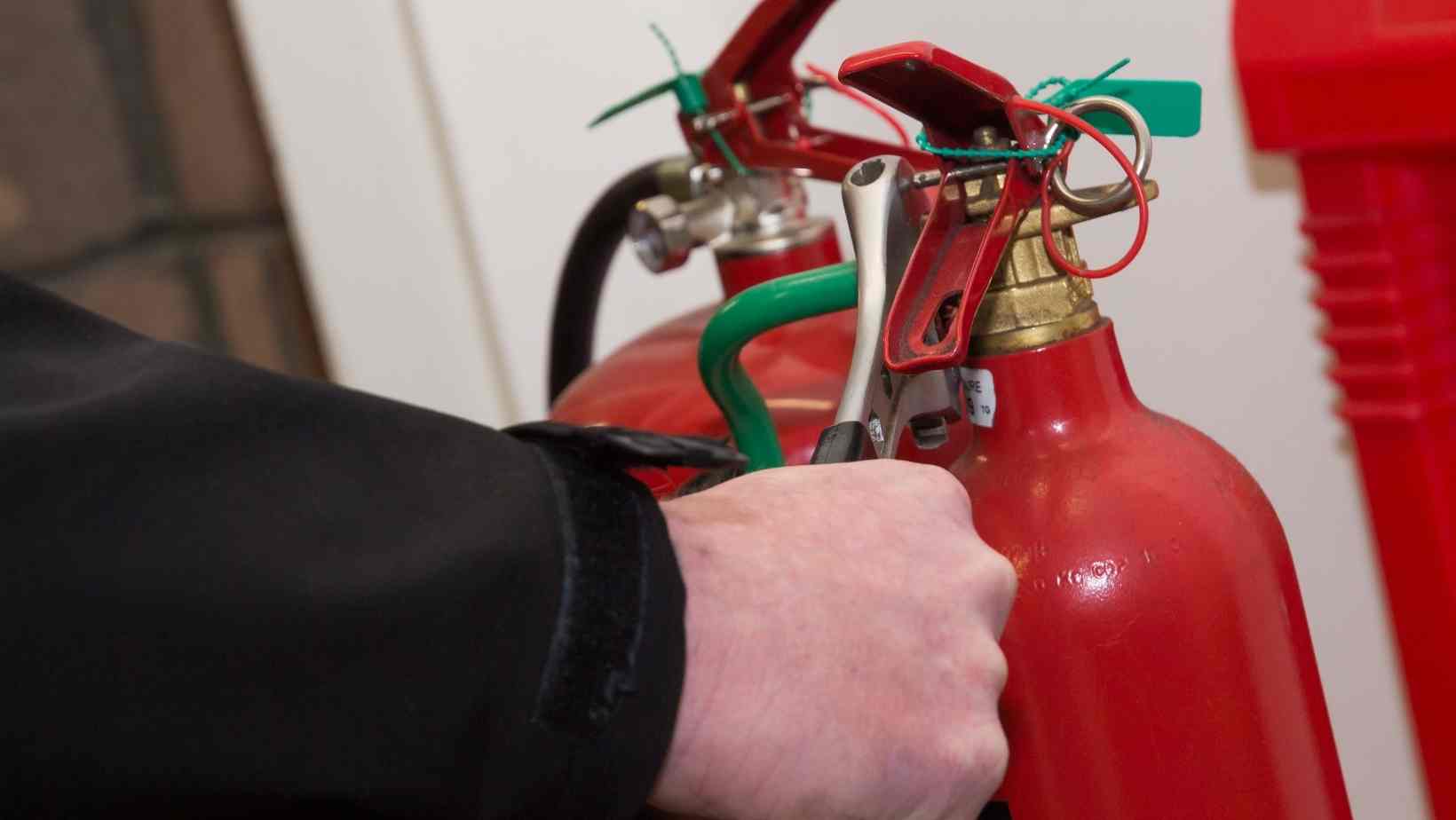
Not just the equipment but also walkways and workstations should be clean and clear to prevent falls and other serious accidents. Any machinery being used should be in proper working order, and it should be fixed or replaced if broken, malfunctioning, or dirty. Regular inspection of equipment is necessary. Note that there are specific standards for when there are vehicles used in the workplace, like forklifts.
Fix violations
After a thorough inspection, violations that were found in the process should be remedied as quickly as possible, and they should be posted in the area. Display OSHA posters so that everyone can see them and understand them. Remember that the poster should be available in English, Spanish, and other necessary languages. Make sure you find what applies to your organization on the OSHA website and follow every applicable standard.
The safety of your facility and employees is what’s most important. The OSHA requires employers to provide their employees with a safe workplace, free of recognized hazards likely to cause serious physical harm or death. Another thing would be for employers to keep a thorough record of all workplace illnesses and injuries, and they should report them on time.
Perform a job hazard analysis
The goal for a JHA is to identify dangers in the workplace before they occur. Note that winter usually introduces unique unprecedented hazards, so it’s important to be well prepared before winter arrives. According to the Bureau of Labor Statistics, employers reported 2.7 million injury and illness cases in 2020. So, it’s important to consider how your employees’ normal tasks, work environment, and tools may need to change.
Conduct a walk-through and focus on one job at a time so you can determine work areas that could pose new hazards. Remember to always include your employees in the job hazard analysis to prevent the change of oversight. Assign protective controls, meaning determine what’s needed to provide an extra safeguard for dangerous tasks and areas. Equip work areas with supplies like absorbent pads and pipe and roof leak diverters to combat hazards.
In closing
Protect your facility and employees against potential hazards with safety solutions that you can easily add to your safety program. Employees should understand how to work safely when threats approach and need to be trained properly. Communicate well and post reminders about new work procedures to ensure overall safety.